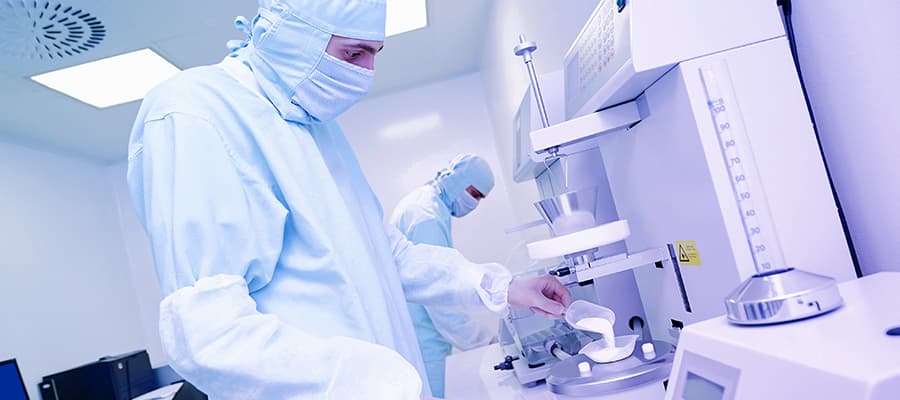
In the highly regulated life sciences industry, quality management and manufacturing professionals face an array of challenges that can hinder operational efficiency. One of the most critical operational aspects that can make or break a pharmaceutical, nutraceutical, or other batch process operation is recipe management in manufacturing. This blog post examines the challenges associated with recipe management in manufacturing and shows how modern digital manufacturing solutions can streamline processes, ensure compliance, and drive operational excellence.
Recipe management in manufacturing involves handling a wide range of data and activities that include:
- Raw material specifications.
- Process parameters.
- Equipment settings.
- Quality control tests.
The sheer complexity of managing hundreds or even thousands of recipes, along with the constant need to update and maintain them, presents countless challenges for quality management and manufacturing professionals. The following are just a few of the many complexities that must be effectively navigated for recipe management to be effective.
- Data Integrity and Version Control:
To ensure accurate and reliable production processes, maintaining data integrity and version control is crucial in recipe management in manufacturing. A minor error or inconsistency in a recipe can lead to batch deviations and sometimes even be responsible for triggering costly product recalls or even jeopardizing patient safety. Manual, paper-based systems are notorious for their susceptibility to errors, oversight, and version control issues.
- Regulatory Compliance:
Life sciences manufacturing is governed by stringent regulations like the current good manufacturing practices (cGMPs) enforced by the U.S. Food and Drug Administration (FDA). Compliance with these regulations demands accurate and up-to-date recipe management to ensure product quality, traceability, and adherence to standard operating procedures. Manual or outdated recipe management software systems can make it difficult to achieve and demonstrate compliance, exposing organizations to regulatory risks.
- Lack of Real-Time Visibility and Collaboration:
Recipe management in manufacturing also requires effective communication and collaboration between various stakeholders such as R&D, production, and quality assurance teams. Without real-time visibility into recipe statuses, progress, and changes, decision-making and issue resolution can be hindered, leading to delays and production inefficiencies.
To address the challenges of recipe management in manufacturing, recipe management software providers have developed and are continually refining innovative, comprehensive, and purpose-built solutions. A proven recipe management software solution can give you the advanced tools and functionality your organization needs to streamline processes, ensure compliance, and enhance operational efficiency. Below are some of the major benefits manufacturers get by implementing digital manufacturing solutions for recipe management.
- Centralized Digital Repository:
A modern recipe management software solution will replace your manual, paper-based processes with a centralized digital repository that securely stores and organizes all recipe-related data. With easy access and search functionality, quality and manufacturing professionals can readily locate and update recipes, ensuring data accuracy and version control.
- Automated Workflows and Approvals:
With automation, a reliable recipe management software can eliminate the need for manual routing and tracking of recipe change requests. This ensures that all changes go through the appropriate review and approval processes, which reduces the risk of errors and facilitates compliance with regulatory requirements.
- Real-Time Collaboration and Visibility:
Robust recipe management software incorporates collaboration capabilities that allow stakeholders to work together in real time. Notifications and alerts can be easily established, enabling instant communication about recipe changes, approvals, and other critical updates. With a holistic view of recipe statuses, stakeholders have the visibility they need to make informed decisions and resolve issues promptly.
Conclusion
Recipe management in manufacturing entails a complex combination of processes that demand precise control and adherence to regulatory requirements. Manual, paper-based systems aren’t capable of meeting the challenges and demands of the modern life sciences industry. The advanced, purpose-built recipe management software solutions now on the market offer comprehensive systems that enhance operational efficiency, streamline processes, simplify collaboration, and ensure compliance. By implementing a modern digital manufacturing solution, manufacturing and quality management professionals can unlock new levels of productivity, reduce risks, and achieve excellence in their operations.
To learn more about MasterControl's recipe management software and how it can help you navigate the complexities of recipe management in manufacturing, visit our Manufacturing Recipe Management System page or contact our team of experts today.
James Jardine is the editor of the GxP Lifeline blog and the marketing content team manager at MasterControl, Inc., a leading provider of cloud-based quality, manufacturing, and compliance software solutions. He has covered life sciences, technology and regulatory matters for MasterControl and various industry publications since 2007. He has a bachelor’s degree in communications with an emphasis in journalism from the University of Utah. Prior to joining MasterControl, James held several senior communications, operations, and development positions. Working for more than a decade in the non-profit sector, he served as the Utah/Idaho director of communications for the American Cancer Society and as the Utah Food Bank’s grants and contracts manager.